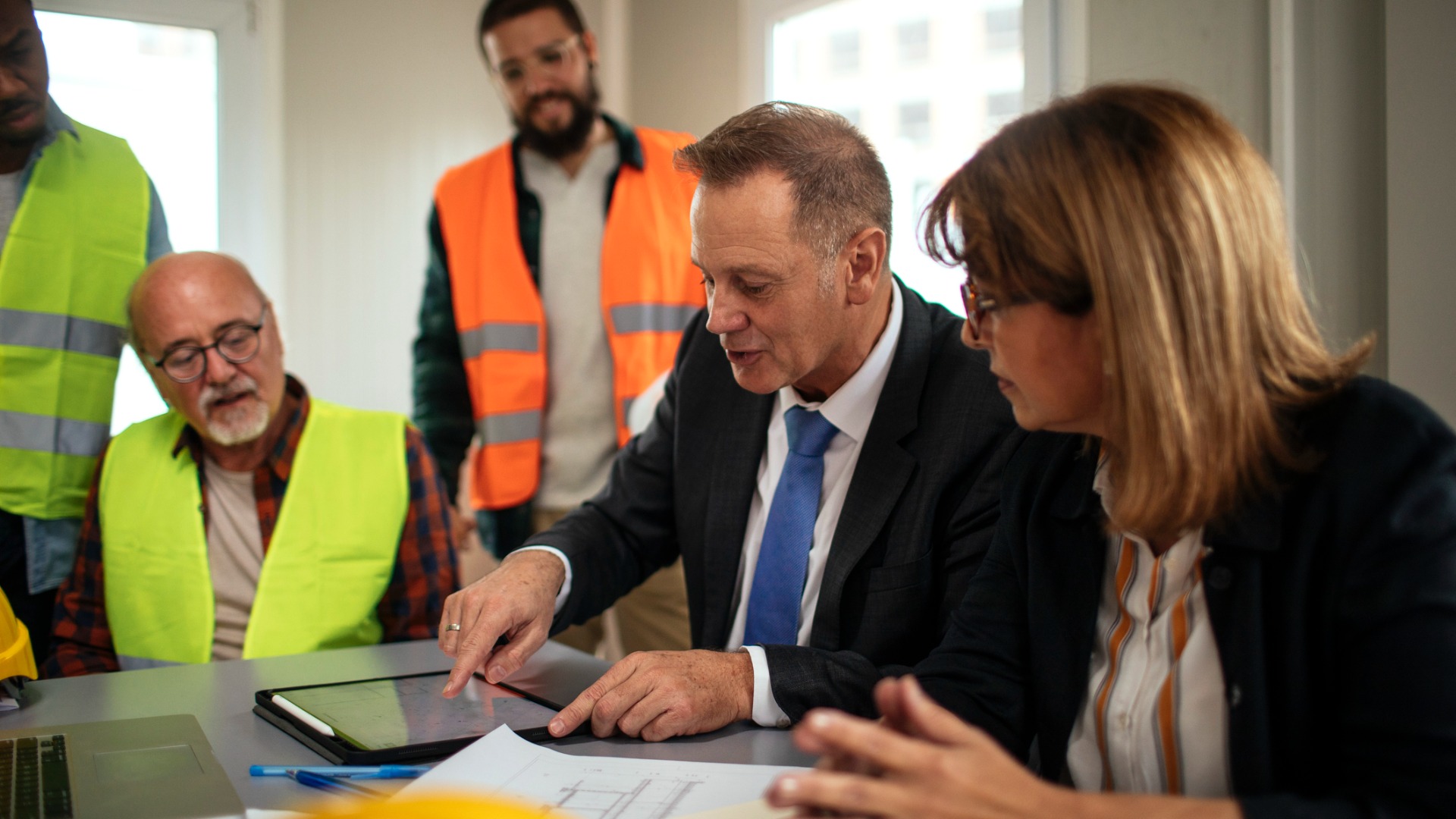
When you purchase a generator, you know that the generator itself should have safety certifications. But what about the company supplying you with it? You may not realize that generator suppliers can and should have various safety certifications from national and local organizations. Your certified generator installer is best equipped to properly and of course, safely install your generator. Certified generator mechanics are necessary to maintain, test, and repair your equipment.
So, which certifications should you be looking for when you are choosing a generator supplier? In part, it depends on your locality, but here are some of the best certifications and other information that you need to know to assess your generator supplier.
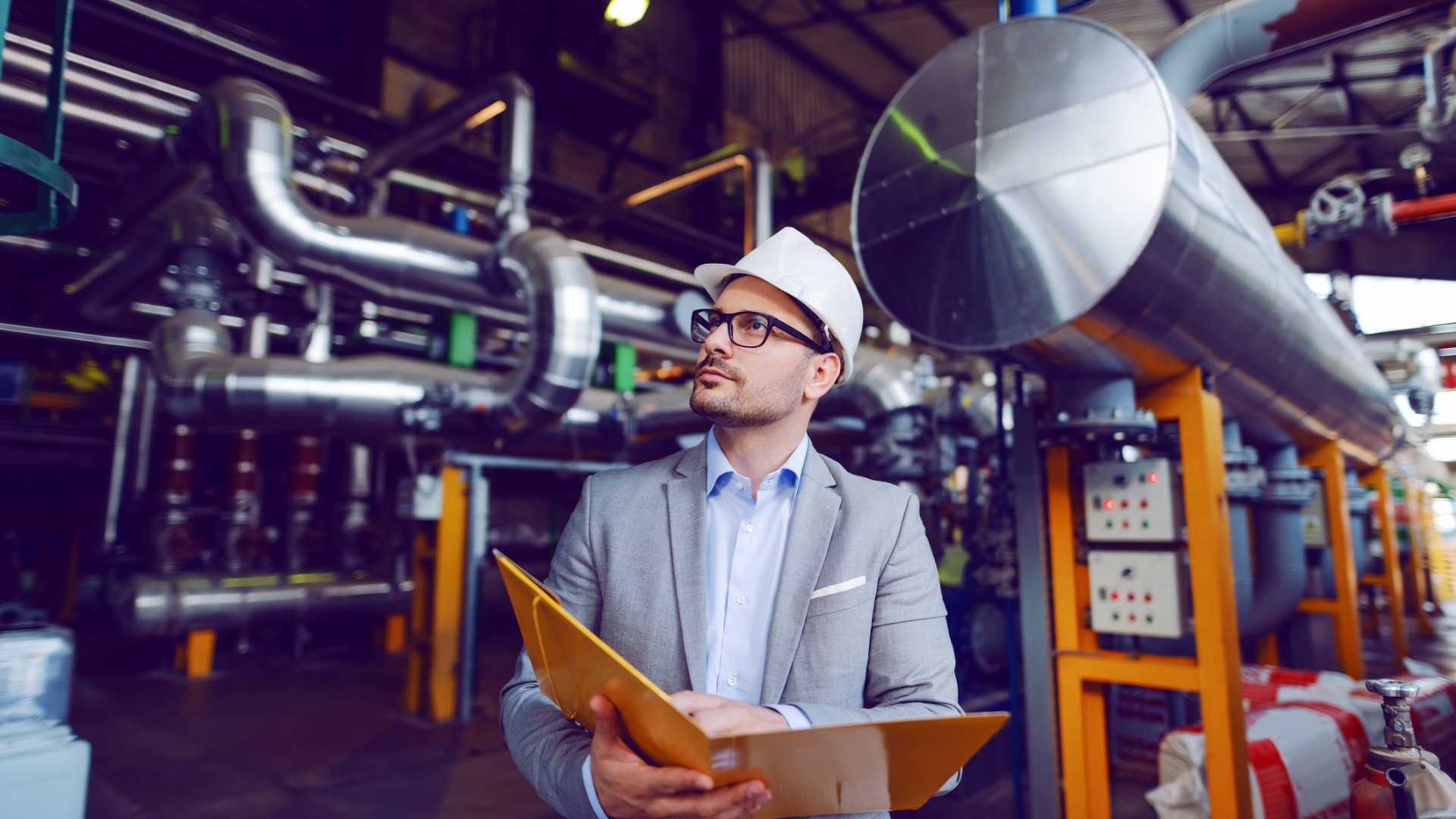
Industrial operations are reliant on their power supply to continue functioning. So how do you ensure that your power supply will continue to operate properly? Especially your backup generators—which you don't use regularly. Load bank testing is an essential part of the picture and critical to truly understanding how your power supply is performing and how an emergency power supply would perform if called upon. Below, we share several reasons why your industrial generators require load bank testing.

Your generator is not just essential equipment for your operation; it also represents a significant investment. Like anything that is both critical and expensive, you want to ensure that you get the most value out of your power generator, and that means following its maintenance schedule to the letter. Better-maintained generators run smoother for longer and more efficiently too. In addition, you’ll avoid repair and replacement costs. That is, if you can give your specific generator the maintenance it needs.