Natural Gas Compression: Reciprocating Compressors vs Screw Compressors
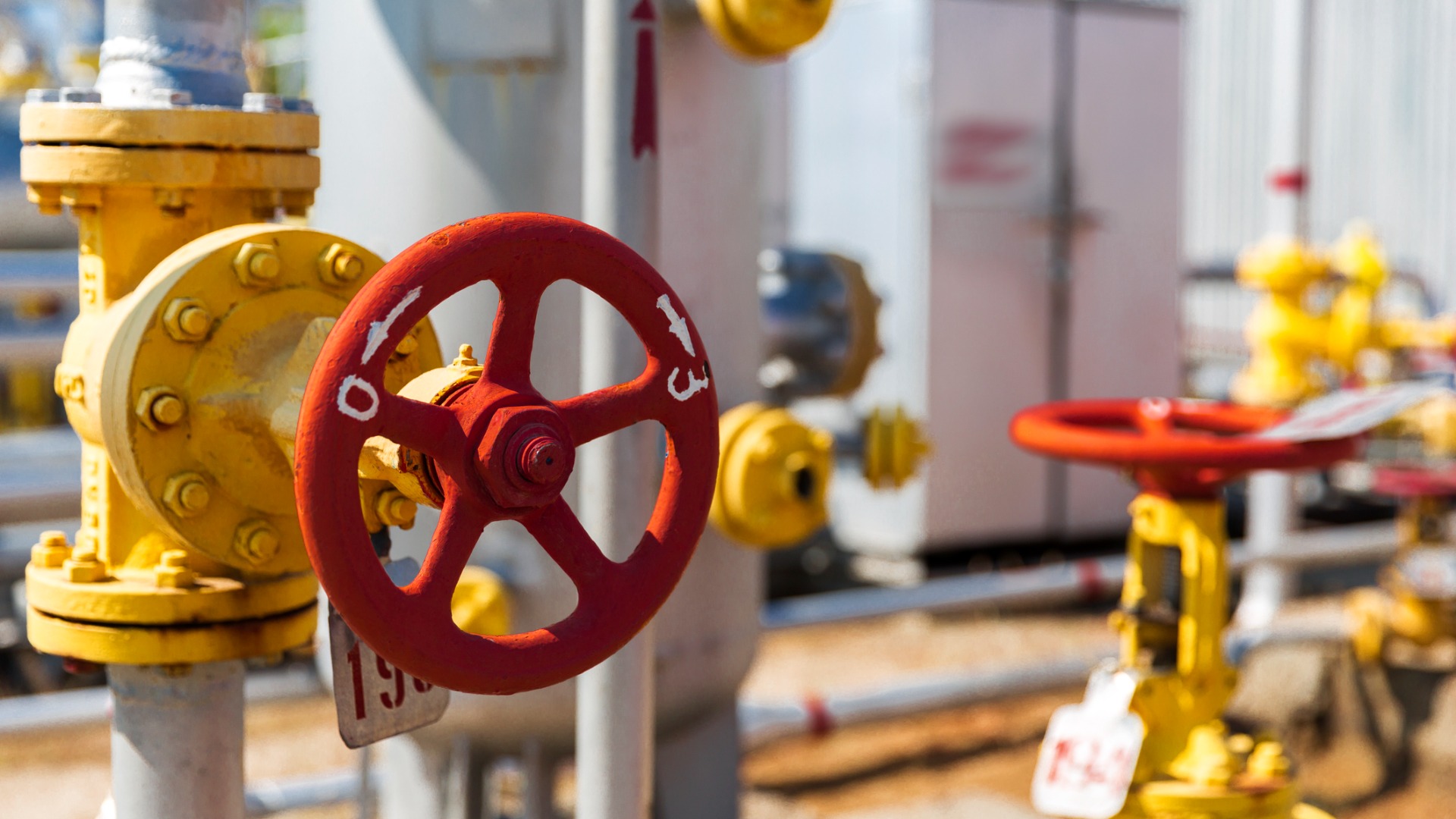
Natural gas arrives to you compressed, that is, stuffed into a space much smaller than it would naturally fill. Natural gas compression is important for many reasons, including safety and ease of transport. But, when it comes to compressing your own gas to fuel your facilities or equipment, the oil and gas industry has two major options: reciprocating compressors and screw compressors.
In this article, we’ll go over why you or your supplier must compress natural gas, the two methods of compression, and why one might be better for your purposes.
Why Does Natural Gas Need to be Compressed?
Compressed natural gas (CNG) is compressed to less than one percent of its original volume. Why do we compress this gas so much? There are several different stages where natural gas may be compressed and many reasons for this work. The times that natural gas may be compressed include:
- During Production: To supply the most gas, producers need to start compressing the gas right at the well. Suppliers inject the already-compressed gas into the well, which causes more of the unprocessed liquid gas to rise to the surface. It’s a smart technique that helps producers make the most of our natural gas reserves, which are precious natural resources.
- Before Transportation: Next, the collected natural gas needs to make its way out to your facility or your fuel tank. Compressing the gas helps ensure that it will make the journey through miles and miles of pipe safely and efficiently. As it reaches its destination, the gas will lose compression, just like liquid running through your pipes loses heat. So, producers need to ensure they create enough pressure for the gas to get where it needs to go.
- Before Storage or Use: To be safe, there needs to be less liquid in natural gas, which means pressurizing it to ensure it is all in gas form. So, the final stage of compression is all about meeting safety standards and ensuring that the gas is in a usable state.
There are two types of compression, but regardless of which is chosen, two main things need to be accounted for during compression. First, natural gas must be free of impurities and particulates before extraction. The producer will handle this before the first compression.
Also, the process generates heat at that first compression stage and every subsequent compression event. Therefore, you must have a mechanism to remove heat when compressing a gas.
The other reasons for compressing natural gas include:
- Improve Safety: Natural gas is more dangerous when in liquid form than when it’s a gas. In order to meet consumer safety regulations and other safety laws, it needs to be compressed to specific pressures before use.
- Movement: Compression, and the release of that pressure, is the mechanism by which gas is transported through pipelines. Compressor stations add the energy that moves the gas, and a different size compressor is needed depending on how much gas is being transported.
- Enable Storage: Not only is it safer to store gas in the form that it can be used—as a gas and not a liquid, but it is also cheaper this way. When compressed, we can store much more gas in a small container. In fact, if we left gas uncompressed, we’d need storage tanks roughly one hundred times the current tank size just to store the same amount of gas.
What is Reciprocating Compression?
Reciprocating compression is often done in three stages. First, it uses a piston and positive displacement as its technique to compress the gas. What happens here is that the gas is drawn into the compression cylinder, the pistons apply the positive displacement to reduce the volume of the gas, and then it is released.
Often, reciprocating compressors will start by getting the gas up to a certain level of pressure, then sending it to be cooled, and then compressing it to a higher pressure. Then the gas is cooled again and finally compressed to its final pressure. This may be as high as 1200 PSI, even though the first stage only increased the gas to about 155 PSI. As you can see, this is a huge jump in pressure.
What is Screw Compression?
Screw compression is a much simpler process than reciprocating compression. However, it cannot compress the gas to the same pressure as reciprocating compression. Both require accurate and well-designed instruments to ensure that the gas does not leak and to move the heat away from the gas as it is being compressed.
The screw compression process runs the gas through threads, where screws or rotors shrink the space and apply pressure. This creates some heat and increases the pressure of the gas to some degree. However, screw compression is normally used for small applications where you need a lower volume of natural gas at a lower pressure.
Which Compressor Should You Choose?
That depends purely on your needs for the output of gas and the pressure the gas needs to be. For high-volume, high-pressure compression, you or your supplier will want to use reciprocating compression, typically in a three-stage model.
For lower pressure and lower output compression, screw compression is a practical choice. For example, screw compressors are ideal for Vapor Recovery Units (VRU).
Consult with an Expert
There is more to compression than we’ve discussed here, including gas liquids extraction, liquids fractionation, and much more. So how do you ensure you’re compressing it properly for your needs?
You don’t need to make your compression decisions alone. The experts at 24/7 Compression can guide you in choosing the right compressor for your pressure and volume needs. We offer new build compressor packages, rental packages, used compression packages, and other services related to gas compression. Reach out to 24/7 Compression to discuss your industrial needs today.