
Methane, or natural gas, is a clean-burning fuel that is being more widely adopted due to its lower carbon emissions. This is occurring in sectors like heavy industry, power generation and transportation. In fact, natural gas has several advantages over diesel as a fuel for transportation. Keep reading to find out what they are.
1. Cost-Effectiveness
Natural gas is significantly cheaper than diesel, making it a more economical choice for businesses, especially those operating large fleets of vehicles. The lower fuel costs associated with natural gas can lead to substantial savings over time, which is particularly beneficial for industries that rely heavily on transportation.
2. Reduced Greenhouse Gas Emissions
Natural gas emits fewer greenhouse gases compared to diesel when burned. This reduction in emissions is crucial for businesses aiming to lower their environmental impact and adhere to stricter regulations concerning air quality and climate change. By switching to natural gas, companies can achieve a cleaner operation that's more sustainable in the long run.
3. Improved Air Quality
Apart from emitting fewer greenhouse gases, natural gas also produces less particulate matter and nitrogen oxides than diesel. This leads to improved air quality around the areas where natural gas vehicles are used, which is beneficial for public health and the environment.
4. Energy Security
Using natural gas can contribute to energy security by diversifying the energy supply. Since natural gas is abundant in many regions, relying on it reduces dependence on imported oil, which can fluctuate in price and availability due to geopolitical factors.
5. Quieter Operations
Vehicles powered by natural gas typically operate more quietly than those running on diesel. This reduction in noise pollution is an added benefit, making natural gas engines ideal for use in urban areas and during night-time operations, where noise might be a concern.
6. Compliance with Emissions Regulations
As regulations on emissions become stricter, switching to natural gas allows businesses to comply more easily with these laws. Natural gas vehicles meet many of the current emissions standards required by governments worldwide, helping companies avoid penalties and potential restrictions.
7. Potential for Renewable Integration
Natural gas provides a pathway to incorporating renewable energy sources. Biogas, which can be produced from organic materials, is compatible with existing natural gas infrastructure. This makes it an attractive option for companies looking to invest in renewable energy solutions without overhauling their current systems.
Why Is Natural Gas Considered The Best Fuel For Transportation?
Natural gas is considered to be the best hydrocarbon fuel for transportation due to its low cost and low carbon emissions compared to gasoline, diesel, and coal. Natural gas is also an abundant resource and is domestically produced, making it a reliable source of energy for transportation purposes. Additionally, it is more energy-efficient than diesel, which results in higher fuel economy and lower operating costs overall.
Learn more about the benefits and advantages of natural gas in our blog!
Rent or Buy the Natual Gas Equipment You Need
Need industrial equipment for oil and gas applications? 24/7 Compression is here to support you! We offer natural gas compression equipment and retrofit services for industries across Western Canada. Contact us today for more information.
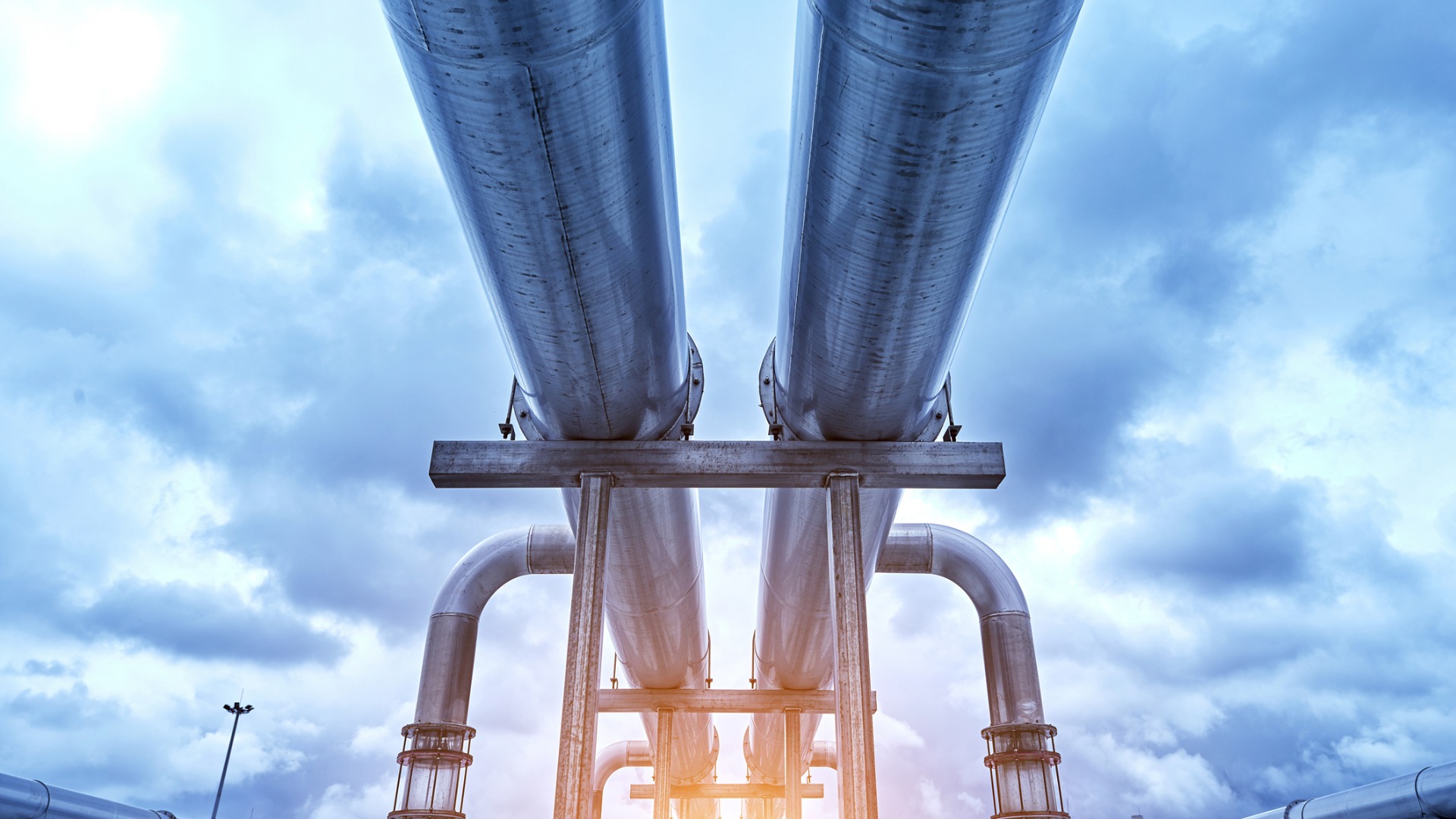
Natural gas is a vital resource for many industries in Canada, and its importance is only set to grow in the coming years. As businesses and governments look for cleaner and more efficient ways to power their operations, natural gas is emerging as a leading contender.
But what exactly is natural gas, and how can it be used? In this article, we will answer some of the most frequently asked questions about the future of natural gas in Canada.
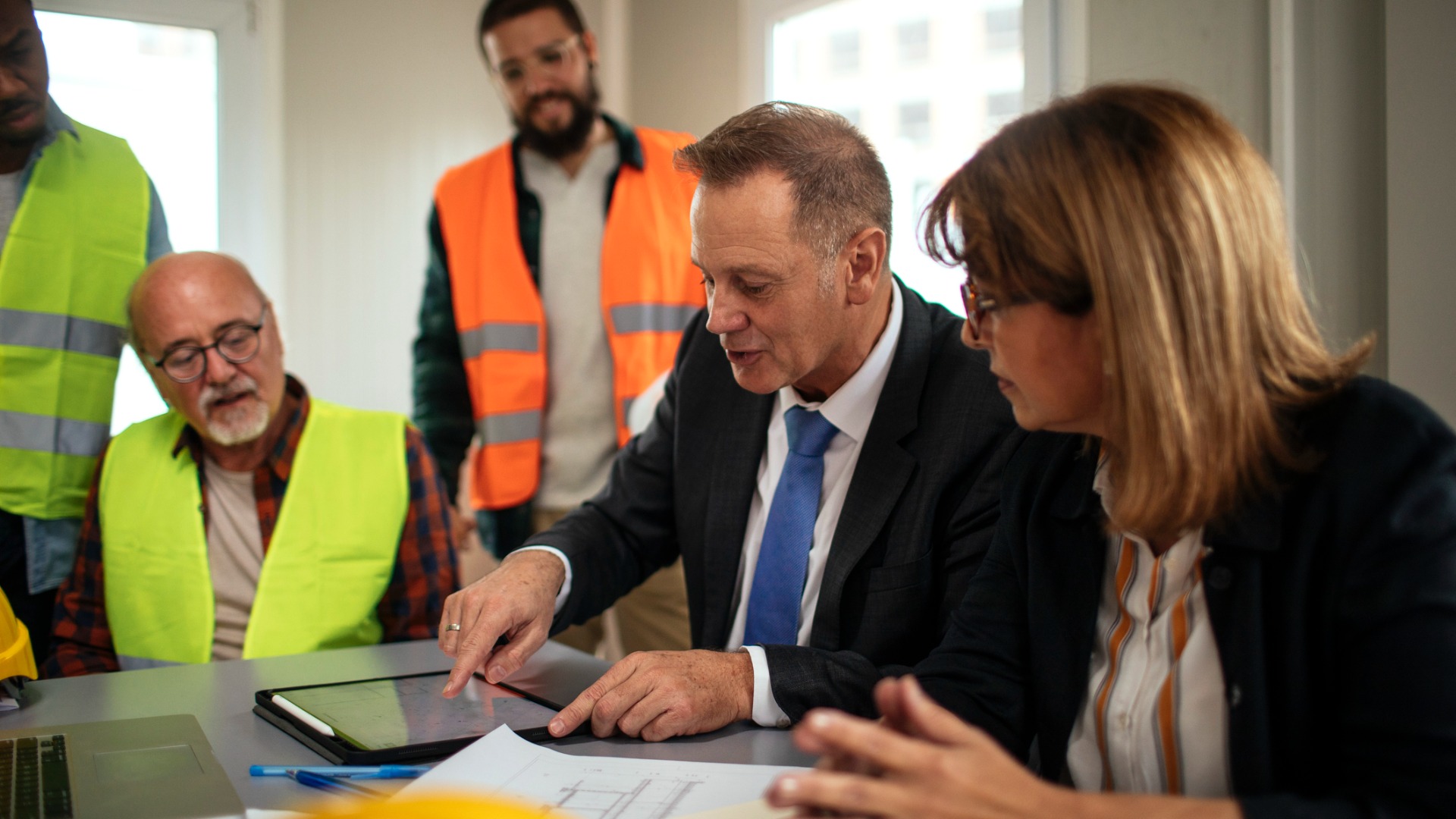
When you purchase a generator, you know that the generator itself should have safety certifications. But what about the company supplying you with it? You may not realize that generator suppliers can and should have various safety certifications from national and local organizations. Your certified generator installer is best equipped to properly and of course, safely install your generator. Certified generator mechanics are necessary to maintain, test, and repair your equipment.
So, which certifications should you be looking for when you are choosing a generator supplier? In part, it depends on your locality, but here are some of the best certifications and other information that you need to know to assess your generator supplier.