Troubleshooting and Tips: Can A Compressor Be Repaired?
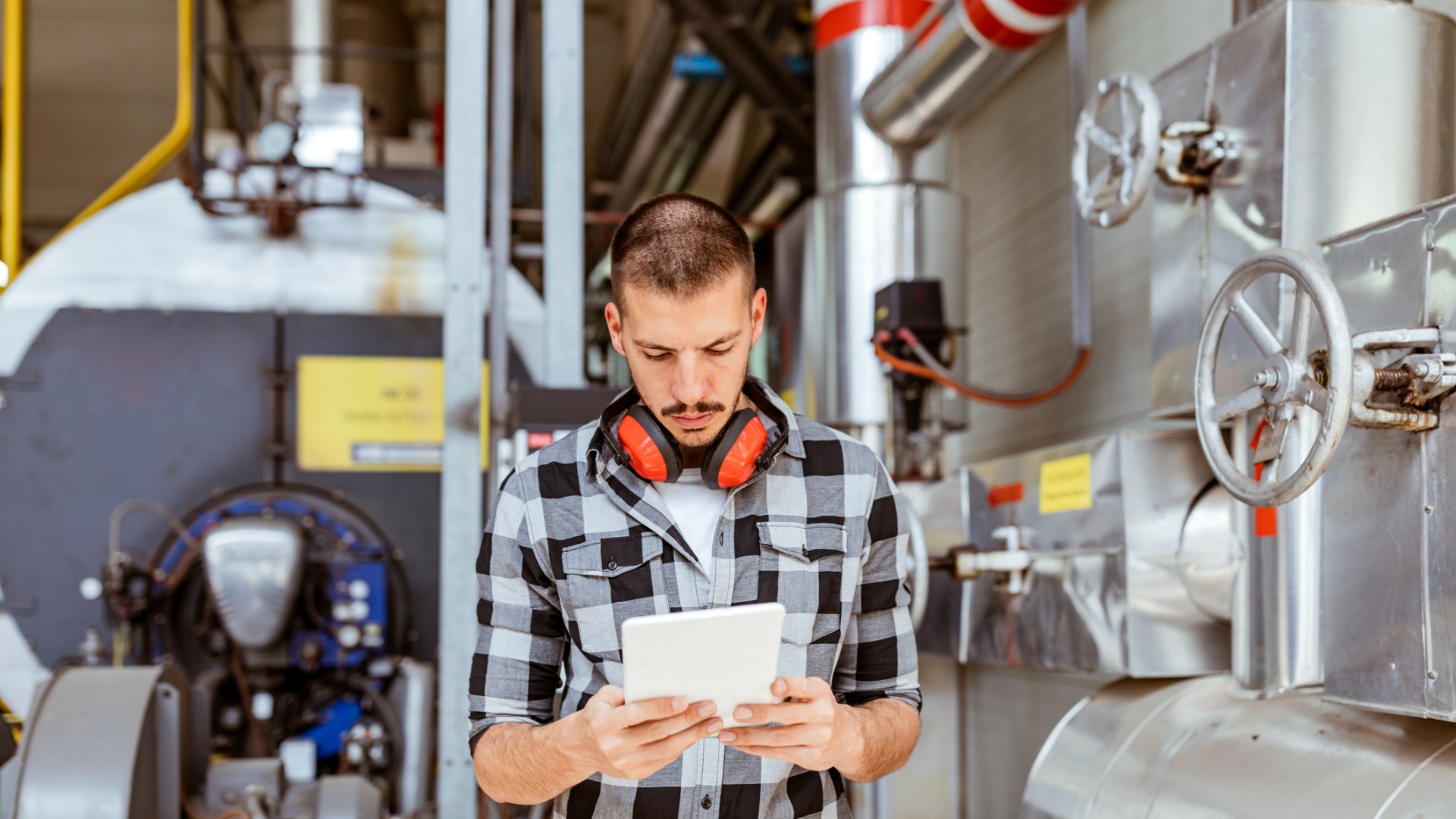
Is the compressor station on your site functioning less than optimally? If so, you can rest assured, knowing you likely won’t require a whole new system. Many common troubles with natural gas compressors can be solved with a quick fix, clean or part replacement.
Compression systems consist of extremely expensive equipment and technology. By keeping your site’s gas compressors in good condition, you’ll improve operation efficiency and reduce downtime so you can get the most out of your investment.
Below, we outline the basics of natural gas compression as well as how to perform compression repairs so you can ensure your operations run as smoothly and efficiently as possible.
How Gas Compressors Work
A natural gas compressor station is a vital component of a gas processing facility. Typically located every 60-100 km along a pipeline, compression stations ensure methane (natural gas) can move efficiently through pipelines to end-users. In addition, compressing cooled methane is the safest way to transport it.
The first step of natural gas compression is the scrubbing process. Scrubbing removes solid, liquid and gaseous impurities from the methane before it becomes pressurized.
The purified gas then travels through yard piping to the compression stations, where computers monitor and regulate the gas flow and increase its pressure by reducing its volume. Once full operational pressure is achieved, the natural gas is released into the pipeline.
Common Issues With Compression Systems
Like all processing systems with multiple moving parts, compression stations require regular maintenance and upkeep to run smoothly. However, sometimes basic servicing isn’t enough, and parts can fail. Below, we discuss common issues with methane compression systems to help you troubleshoot any problems you may be experiencing with your system.
Valve Failures
If your system has shut down unexpectedly, this may be due to a valve failure. Compressor stations have various safety systems in place to protect both workers and the public. These systems include emergency shutdown devices that prevent gas from leaking along with other dangerous situations.
Often, a shutdown is caused by a defective valve. Valve springs can become worn, preventing the valve from operating properly and leading to malfunctions in the compression system.
Fluid Leaks
Methane is a highly flammable gas but is virtually undetectable due to being colourless and odourless. Therefore, methane leaks are extremely hazardous and may trigger a shutdown.
Excessive Noise
Even under normal operating conditions, gas compressors are a significant source of industrial noise. However, if your system becomes more noisy than usual or exhibits unusual sounds, this may be a sign that something is critically wrong within the system.
The cause of excessive noise could be as simple as particle build-up on plates, which is easy to fix, or it may be due to a cracked damper plate.
Damper plates are designed to dampen the noise from vibrations in the system. Since these plates are under constant mechanical stress, they are prone to breaking and require frequent replacement.
Not Building Pressure
Properly pressurizing natural gas is crucial for efficient fluid flow. If you aren’t reaching the desired gas pressure, or if it is taking an excessive amount of time to achieve your operational pressure, you should check your valves and seals. Leaks within your system can lead to significant operational inefficiencies, leading to more money lost in the long run.
How to Repair a Natural Gas Compressor
So, can a faulty gas compressor be repaired? In most cases, repairs are simple and to be expected; otherwise, you may need to replace various parts and components. If problems with your gas compressor persist beyond simple repairs, then it may be time to call in an expert technician to assess your system and determine whether your devices are beyond repair or not.
This section outlines some common and simple repairs you can perform to ensure your compressor runs as smoothly as possible.
Replace Consumable Parts
Gaskets, belts, valve plates, and similar parts are prone to cracking, warping and breaking apart since they are subjected to continuous movement and vibrations. Ensure these components are replaced regularly and assess your system frequently to avoid extended downtime if they fail before expected.
Check for Corrosion
If you’re noticing corrosion or warping on any parts within your machine, this should be dealt with as swiftly as possible. In general, corrosion should be minimal; therefore, it may mean the wrong materials are being used in certain areas of the system. Consult with a specialist if you suspect there are unsuitable materials being used in your system.
Clean Pistons
Dirty pistons and valve plates can contribute to excessive noise in the system. Removing and cleaning these parts is generally a simple enough task to keep your machine running smoother for longer.
Check Valve Plates and Seals
Valve plates are notorious for causing problems in gas compressors. Warped or damaged valve plates can lead to leaks in the system as well as failures to reach the desired operational pressure. Ensure valve plates and seals are functioning optimally by inspecting them thoroughly whenever a leak or malfunction is suspected.
Contact a Professional
If a gas compressor repair appears too great for your team to handle, it’s best to contact a compressor maintenance professional to assess your system and potentially make extensive repairs. On the other hand, if your site’s equipment is old and inefficient, it may be best to purchase new parts and components for the best operational outcomes.
At 24/7 compression, we have the equipment, experience and know-how to get your gas compression systems running as smoothly as possible. Contact us today to learn more about what we can offer.